Audi Q3: Repair Information
Shock Absorber Leaks
Shock absorbers are frequently rejected and exchanged
because of leaks. Examinations on the test stand and on the
vehicle have shown that the replacement of a large number of
rejected shock absorbers was not justified.
Slight leaking of oil ("sweating") at piston rod seal is no
reason to replace a shock absorber. A shock absorber damp with
oil is OK under the following circumstances:
- Oil leak (shown screened in illustration) is visible, but
dull, matte and possibly dry from dust
- Oil excretion extends from upper shock absorber connection
(piston rod oil seal) no further than lower spring plate
-arrow-
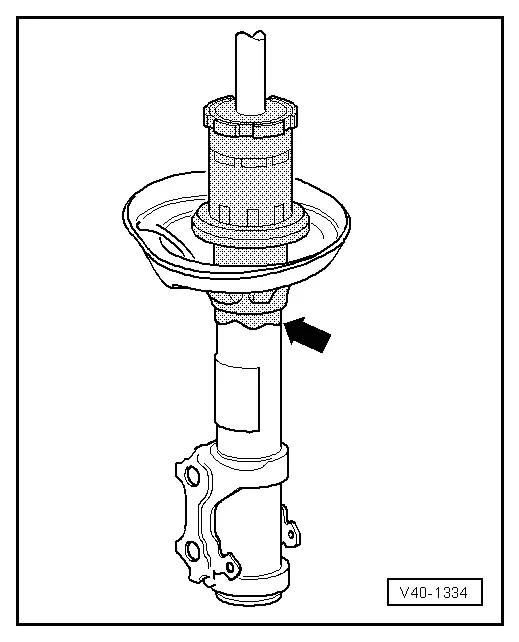
Shock Absorbers, Checking when Removed
Defective shock absorbers are noticeable when driving due to
loud rumbling noises - a result of wheel hopping - especially on
poor stretches of road. Moreover, they can be recognized by a
large loss of oil.
Note
Shock absorbers are maintenance-free, shock absorber oil
cannot be topped off.
A removed shock absorber can be checked by hand as follows:
- Push the shock absorber together by hand.
- Piston rod must move with even resistance throughout entire
stroke and without jerking.
- Release piston rods.
- For shock absorbers with sufficient gas pressure, piston rod
returns to initial position automatically.
Note
- If this is not the case, shock absorber must be replaced. As
long as oil loss is not large, the effectiveness represents that
of a conventional shock absorber.
- The damping function is also completely available without
gas pressure, as long as there is no large loss of oil. However,
noise may increase.
Shock Absorbers, Checking on Shock Tester
Shock absorbers can be checked while installed using the
shock tester (shock absorber testing device). The damping effect
can be evaluated based on the dial reading or print-out.
Special tools and workshop equipment
required
- Maha Shock Absorber Tester -VAS1990- or
- Suspension Strut Test Bed -VAS6636- or
- Suspension Strut Test Bed VAS6640 -VAS6640-
Test Prerequisites
- Temperature +10 through +40 ºC (+50 through +104 ºF).
- Driver in vehicle.
- Tire pressure OK.
- Drive vehicle straight onto center of wheel contact plates.
- Front wheels in straight position.
- Parking not engaged, foot brake not activated.
Threshold
Shock absorber condition can only be judged as follows:
- Sufficient damping effect
or
- Insufficient damping effect
Note
- Intermediate values for reduced damping performance cannot
be read out.
- A prognosis on service life is not permitted.
- Measured values that occur with the involvement of the
suspension travel end stops are incorrect.
The following values apply only to the test stands named
above. If the specified values are exceeded, the shock absorber
action has weakened enough that a replacement is recommended.
Example:
Threshold = 70
- a = greater than 70: insufficient damping effect
- a = less than 70: sufficient damping effect
The shock absorber combination installed in the vehicle is
indicated by the corresponding PR number on the vehicle data
plate.
Production Control Number (PR number) explanation. Refer to
→ Chapter "Explanations of Production Control Numbers (PR
Number)".
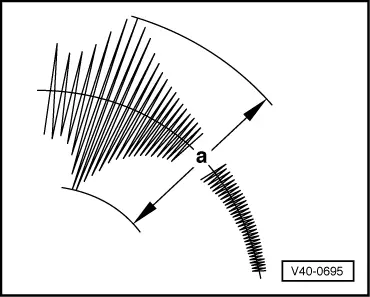
Threshold "a" in mm
Note
- If the readout value is greater than the limit value "a"
(table value): insufficient damping effect ⇒ replace shock
absorber.
- If the readout value is less than the limit value "a" (table
value): sufficient damping effect ⇒ shock absorber does not need
to be replaced.
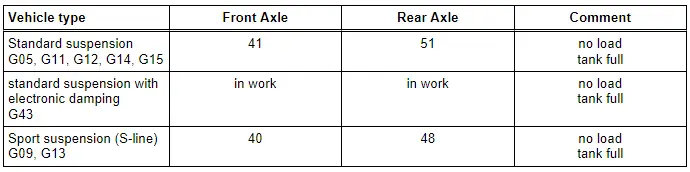
The tires must be "partially loaded" when measuring the tire pressure.
Clean Working Conditions
- Thoroughly clean connecting points and their surrounding
areas before loosening.
- When installing steering gear, make sure centering sleeves
are correctly seated between console and steering gear.
- Place removed parts on a clean surface and cover them so
that they do not get dirty. Use foil and paper. Only use
lint-free cloths!
- Install only clean parts: remove the replacement parts from
their packaging just before installing them.
- Use exclusively lubricants and sealants marked with part
numbers.
- Carefully cover or seal opened components if the repair will
not be done immediately.
General Information
WARNING
If vehicle will be driving on the streets, all
screws and nuts must be tightened properly!
- When installing waxed components, contact surfaces must be
cleaned. Contact surfaces must be free of wax and grease.
- Tightening specifications for non-lubricated bolts and nuts
are given.
- Always replace self-locking nuts and bolts.
- Always replace the bolts and nuts, which are tightened with
an additional tightening angle.
- Welding or straightening operations are not permitted on
load-bearing or wheel-controlling components.
- Always avoid the following actions with coil springs: hammer
strokes, welding beads, applying color identification later.
- Do not perform any welding or grinding (separating work) in
coil spring or suspension strut area! Cover coil spring or
suspension struts if necessary.
- When loosening, removing or installing hydraulic, pneumatic
or electrical line, always make a sketch or take a picture. This
ensures installation is the same as the original.
- If the cable ties, brackets or mounting elements were
removed during the repair procedure, they must be installed at
their original location.
- Lightly coat the splines on the outer joint with assembly
paste before installing the outer joint into the wheel hub.
Refer to the Parts Catalog.
- Never allow the drive axle just to hang loose under the
vehicle or to bend them at the joints.
- Vehicles without a drive axle must not be moved, otherwise
the wheel bearing will be damaged. If a vehicle must be moved,
be sure to note the following:
- Install an outer joint in place of the drive axle.
- Tighten the outer joint to 200 Nm.
- Bonded rubber bushings have a limited range of motion. For
this reason only tighten threaded connections at control arms if
vehicle is in curb weight position. Refer to
→ Chapter "Wheel Bearing in Curb Weight, Lifting Vehicles with
Coil Spring".
- Always replace bonded rubber bushings on both sides of
vehicle.
General Repair Information
A number of generally applicable instructions for individual
repair operations, which are otherwise mentioned at various
points in the Workshop Manual, are summarized here. They apply
to this repair manual.
- Before performing repairs on the electro-mechanical steering
gear, determine the cause of the damage as accurately as
possible using the Vehicle Diagnosis Tester in the "Guided Fault
Finding", "Vehicle Self-Diagnosis" and "Measurement" modes.
Contact Corrosion
Contact corrosion can occur if incorrect fasteners (such as
bolts, nuts, washers, etc.) are used.
For this reason, only fasteners with a special surface
coating are installed.
In addition, rubber or plastic parts and adhesives are made
of non-conductive materials.
If there are doubts whether a part should be used again,
install a new part according to the Parts Catalog.
Please note:
- The use of original replacement parts is recommended, they
are tested and are compatible with aluminum.
- The use of Audi accessories is recommended.
- Damage due to contract corrosion is not covered under
warranty!
Steering Gear
To perform a problem-free and successful steering gear repair, extreme
caution and cleanliness, as well as properly functioning tools are an important
requirement. The usual basic safety precautions also, naturally apply when
carrying out vehicle repairs.
Seals, Sealing Rings
- Always replace seals and gaskets.
- After removing seals, inspect contact surface on housings
and shafts for burrs and damage and repair if necessary.
- Remove all residual sealant of fluid seals from sealing
surfaces, no sealant residue must enter the steering gear
housing when doing this.
Bolts and Nuts
- Loosen and tighten the screw and nut from the covers and
housings diagonally.
- Do not cant but loosen and tighten especially sensitive
parts in diagonal manner in stages, for example servo motor with
control module.
- Tightening specifications for non-lubricated bolts and nuts
are given.
- Always replace self-locking nuts and bolts.
- Always replace the bolts and nuts, which are tightened with
an additional tightening angle.
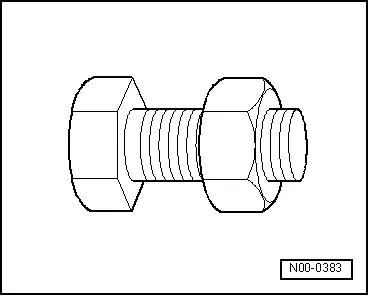
Electrical Components
Surely everyone has been shocked at one time or another when
coming into contact with a metal object. The reason for this is
the build-up of static electricity in the human body. This
charge can lead to functional problems by touching the
electrical components of steering gear.
- Touch a grounded object, such as a water pipe or a vehicle
hoist, before working on electrical components. Do not make
direct contact on connector terminals.
Damaged Threads in Longitudinal Member, Repairing (Subframe to Body)
For the procedure for repairing a damaged thread.
Wheel Bearing in Curb Weight, Lifting Vehicles with Coil Spring
Special tools and workshop equipment
required
- Tensioning Strap -T10038-
- Engine/Gearbox Jack Adapter - Wheel Hub Support -T10149-
- Engine and Gearbox Jack -VAS6931-
Note
All bolts at suspension parts with bonded rubber bushings
must always be tightened in curb weight position (unloaded
condition).
- Bonded rubber bushings have a limited range of motion.
- Axle components with bonded rubber bushings must be brought
into the position they will be in during driving before
tightening (curb weight position).
- Otherwise, the bonded rubber bushing will be stressed
resulting in a shortened service life.
- By raising appropriate suspension using Engine and Gearbox
Jack -VAS6931- and Engine/Gearbox Jack Adapter - Wheel Hub
Support -T10149-, this position can be simulated on the hoist.
- Before starting work, determine the measurement
-a-, for example with tape measure,
from center of wheel to lower edge of wheelhouse.
- Measurement must be performed in curb weight position
(unloaded condition).
- Note the measured values. It will be required for tightening
bolts/nuts.
Before appropriate suspension is raised, vehicle must be
strapped to lift arms of hoist using Tensioning Strap -T10038-.
Note
The vehicle could fall off the hoist if it is not secured.
- Turn the wheel hub until one of the holes for the wheel
bolts is on top.
- Install Engine/Gearbox Jack Adapter - Wheel Hub Support
-T10149- with wheel bolt on wheel hub.
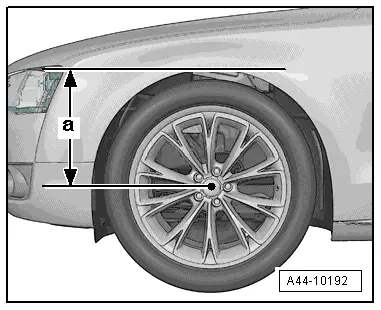
- Lift the wheel bearing housing using the Engine and Gearbox
Jack -VAS6931- until dimension -a-
is reached.
Tightening of the respective bolts/nuts must only occur if
dimension -a-, measured before
installation between wheel hub center and lower edge of wheel
house, has been attained.
WARNING
- Do not lift or lower vehicle with the
engine/transmission jack still under the vehicle.
- Do not leave the Engine and Gearbox Jack -VAS6931-
under the vehicle any longer than necessary.
- Tighten the bolts and nuts.
- Lower the wheel bearing housing.
- Move the engine and gearbox jack away from under vehicle.
- Remove the Engine/Gearbox Jack Adapter - Wheel Hub Support
-T10149-
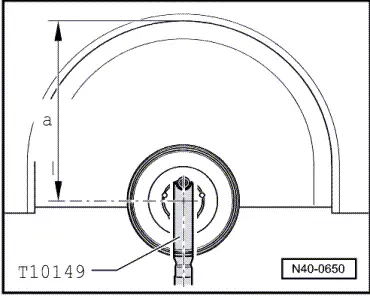
READ NEXT:
Front Shock Absorbers, Venting and Emptying
Method A - Venting through Drill Holes
- Secure gas-filled shock absorber vertically in vise, with
piston rod facing down.
WARNING
Wear
Caution
There is a risk of damaging the subframe threaded
connection threads on the body.
The subframe bolts on the body must not be loosened
or tightened with an impact wrench.
A
SEE MORE:
Caution
It is mandatory for run-flat tires to have a tire
pressure monitoring system in the vehicle.
Installing/Conditions for Using Run-Flat Tires
Caution
It is mandatory for run-flat tires to have a tire
pressure monitoring system in the vehicle.
Because pressure loss
Component Location Overview - Control Modules
Component Location Overview - Control Modules
1 - Vehicle Electrical System Control Module -J519-
Removing and installing. Refer to
→ Chapter "Vehicle Electrical System Control Module -J519-, Removing and
Installing".
2&nb